Rubber Extrusion
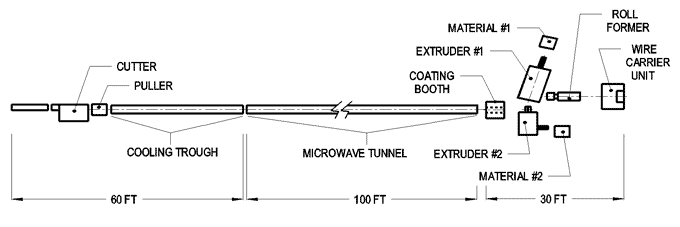
There are two types of Rubber Extrusion processes:
continuous in-line cure and off-line cure.
With the continuous cure in-line process, the rubber is forced through the aperture or die, traveling in a continuous stream directly into and through a ‘curing tunnel’ which uniformly raises the extrudite to the vulcanizing temperature and maintains it there for the entire curing or vulcanizing period. The speed at which the product travels is combined with the length of the tunnel to calculate and control the time-at-temperature of the vulcanizing period.
The stream of newly-cured rubber exits the curing tunnel and enters a cooling trough where the (still) hot rubber is cleansed of residue, picked up in the tunnel and cooled so it can be handled. The extrudite is conveyed through the cooling medium by way of a puller at the end of the extrusion line (which maintains line tension and aids in the overall dimensional stability of the process).
There are four media commonly used to create the ‘curing tunnel’: high velocity hot air, microwave ovens, hot liquid curing medium (LCM) or fluidized bed of glass Ballotini beads. In all cases, the objective of the medium is to quickly bring the continuous stream of rubber up to a pre-set temperature and hold it there until vulcanization is complete.
There are many advantages of continuous curing:
long continuous lengths, speed of manufacture, low labor content, efficient energy usage, space economy and attainable dimensional tolerancing. Another advantage of continuous curing is the flexibility to combine multiple materials including closed cell expanded rubber and metal core. The technology involved in shaping and curing two or three rubber compounds in-line simultaneously, provides the opportunity to develop a wide variety of products for the transportation and general industrial markets.
There are also disadvantages: higher raw material set-up costs, higher overall raw material costs because of the compounding necessary to run through these systems, size limitations owing to the tensioning necessary to get the product pulled through the entire system, and certain shapes and radii that cannot be attained through this method of curing Closed-cell expanded rubber is a typical material that needs to be run through a continuous cure system.
In off-line Rubber Extrusion, autoclaves are used to promote the curing process. During the autoclave curing process, shapes created by forcing ‘warm rubber’ through an aperture or die, are exposed to high pressure steam, brought to the specific compound’s vulcanizing temperature and held there until the chemical reaction is complete.
Prior to the batch entering the autoclave for curing, each uncured tubular shape is forced over a mandrel and the rubber maintains the distinct shape imparted by the mandrel as it cures. This is very useful when making well-made radiator hoses, fuels tubes and other formed hoses.